Me revoilà, j'étais au salon du Bourget.
Aujourd’hui je vais vous parler des jauges moteurs. Toutes fonctionnent avec des servomoteurs et une carte USBservo de IOcard (opencockpit). Pour ceux qui pour la première fois, on construit une telle jauge c’est un enchantement de voir une aiguille tourner à partir des impulsions électriques de l’ordinateur.
Encore une fois, je n’ai rien inventé. Plusieurs simmeurs se sont adonnés à la tâche, malheureusement, à ma connaissance, il n’en reste pas beaucoup sur la toile.
Rendons à César ce qui appartient à César je citerai l’excellent site des 2 Pierre :
http://www.simubaron.fr/panneau_moteurs.htm
ou celui de Scott Hendry
https://www.flickr.com/photos/40066091@ ... 3119115601
Sans oublier ceux, non moins excellents, de Mameloose : ces fameux tutos. Pour ce qui nous concerne, l’utilisation d’une carte USBservo
https://www.flight-pilote.com/topic-121 ... age-1.html
Voici comme introduction le panneau des jauges moteurs.
les trous pour accueillir les jauges sont de 55mm. On trouve facilement des scies cloche de cette dimension dans les magasins de bricolage.
Afin de positionner les jauges sur la plaque d'alu, j'utilise un tracé d'Autocad imprimé à l'échelle 1/1/ que je colle sur celle-ci (colle repositionnable). Les découpes et les perçages s'en trouvent facilitées.
Pour information voici un site où vous pourrez trouvez des plaques d'alu et autre matériaux.
http://www.blockenstock.fr/
Et voici le verso:
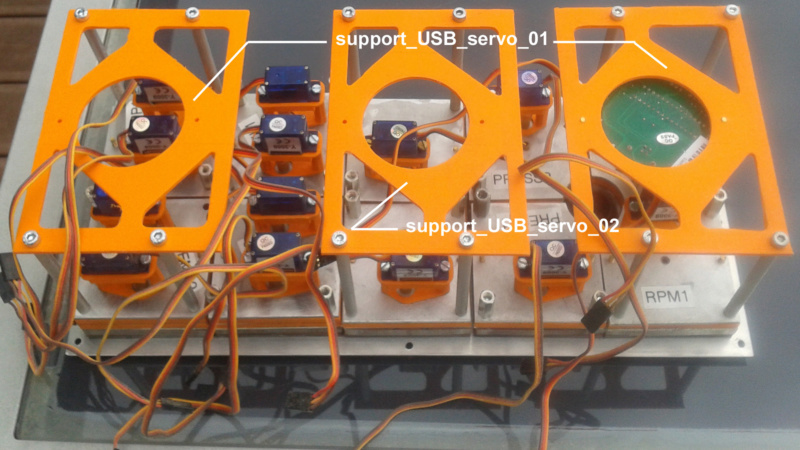
vous pouvez apercevoir en vert la carte USB servo, il y en aura trois.
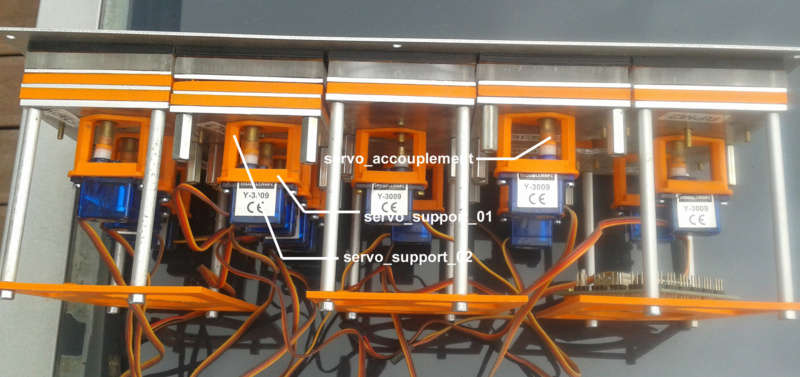
Maintenant, je vais vous détailler la construction d’une jauge simple ou double aiguille.
Pour commencer le RPM
Comme moteur d’entrainement j’utilise des servo moteurs Modelcraff Y-3009, cité en mode indicatif, car vous pouvez utiliser bien d’autre. Je vous donne celui là car tout ce qui suit correspond à ses dimensions.
Normalement un servo à un débattement compris entre 180 et 270°, ce qui est souvent insuffisant pour une course d’aiguille. Surtout qu’il vaut mieux garder une marge de sécurité pour ne pas aller en butée. On va donc, pour multiplier l’angle de rotation des engrenages.
La première chose à savoir c’est qu’un engrenage, se caractérise par son nombre de dents (c’est évident) et son module qui pour faire vite c’est approximativement la largeur d’une dent.
Pour ce qui nous concerne nous resterons dans les modules 0.5 à 1. Là aussi pour faire vite, une roue dentée de 40 dents aura un diamètre de 20mm pour un module 0.5 pour un diamètre de 40mm pour un module 1. Ces dimensions conditionnent aussi les dimensions des instruments.
Maintenant où les trouver : il existe bien entendu plusieurs sites. Je vous en cite un : HPC
https://shop.hpceurope.com/fr/categorie.asp?faId=4&caid=4&produit=Engrenages%20%C3%A0%20denture%20droite
A vous de choisir la matière de l’engrenage. Un autre aspect à méditer est l’épaisseur du pignon et surtout la dimension de son alésage (le trou), ce seront donc des dimensions à rectifier. Un alésage trop petit peut facilement être agrandi avec une perceuse, diminuer un alésage trop grand s’avère plus délicat. L’usage d’un tour à métaux facilite grandement ces manipulations.
L’autre solution est de les fabriquer si vous possédez, comme moi un tout et une fraiseuse.
Malgré le coût des fraises spécifiques à la taille des engrenages, moyennant quelques astuces et malgré le temps passé, cette méthode peut s’avérer rentable suivant le nombre de pignons que vous souhaitez utiliser (donc suivant le nombre d’instruments que vous allez construire) vu le coût marchand de ces pièces.
Je vous ai déjà décrit ma méthode dans cette rubrique :
http://www.aircockpit.com/viewtopic.php?f=64&t=6356&p=83453#p83453
Pour ceux qui veulent de plus amples explications, je suis à votre disposition.
Une autre méthode c’est l’imprimante 3D, machine qui s’est largement démocratisée, que l’on trouve de plus en plus chez les maquettistes et dans les FabLab.
Par contre il faut les modéliser. Pour ma part j’utilise FreeCAD, qui est un logiciel en open source et entièrement gratuit.
Dans le FreeCAD 0.16 il suffit d’être en Part Design
Puis dans la fenêtre Part Design choisir Involute Gear puis cette fois-ci le module et le nombre de dents et le tour est presque joué. J’en ai imprimé en module 0.75 et 1 sans problème de transmission par la suite.
Pour info, avec cette fonction on peu fabriquer des boutons moletés.
Voilà pour les engrenages, c’était un peu long, mais je pense nécessaire.
Voyons maintenant, en images,les détails de fabrication de ce genre d’instrument.
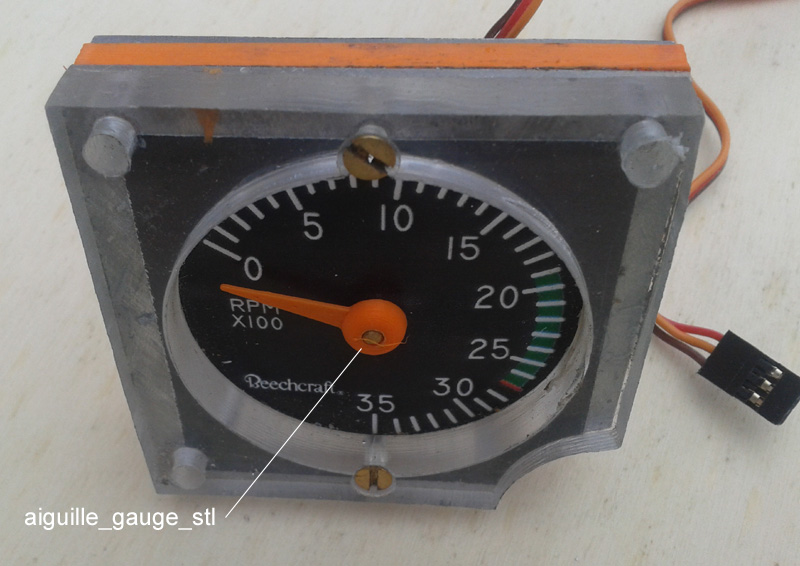
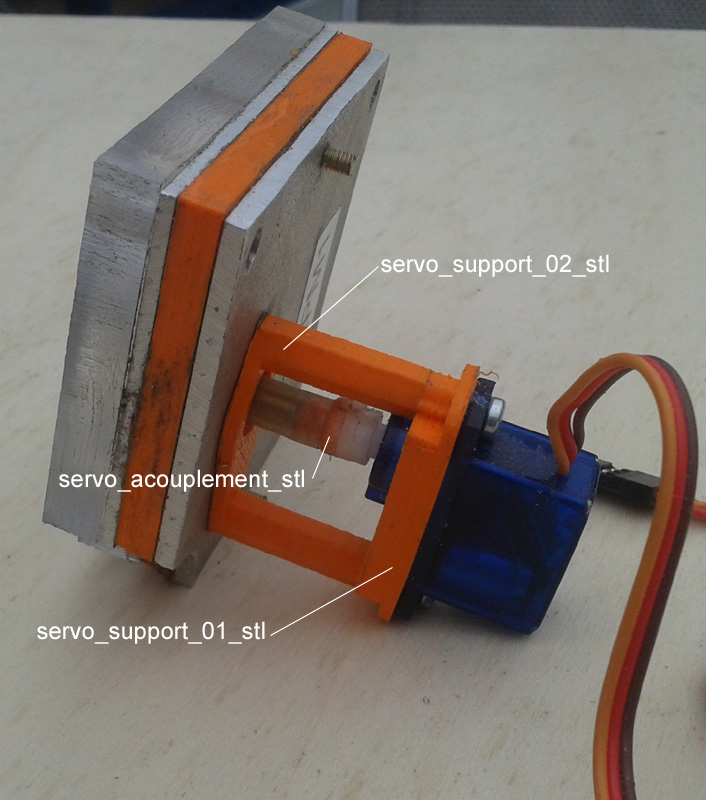
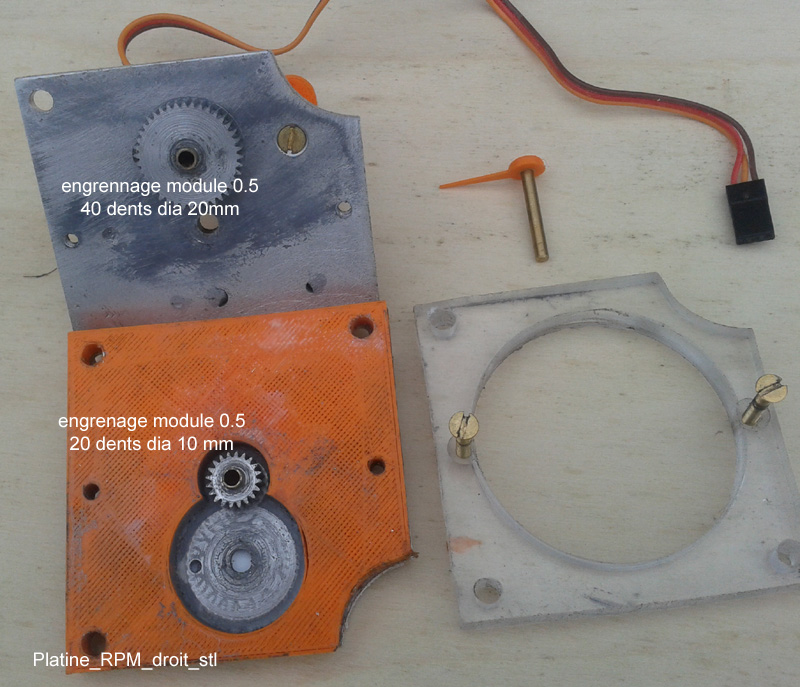
Pour les jauges à 2 aiguilles, que voici, ce n'est pas plus compliqué.
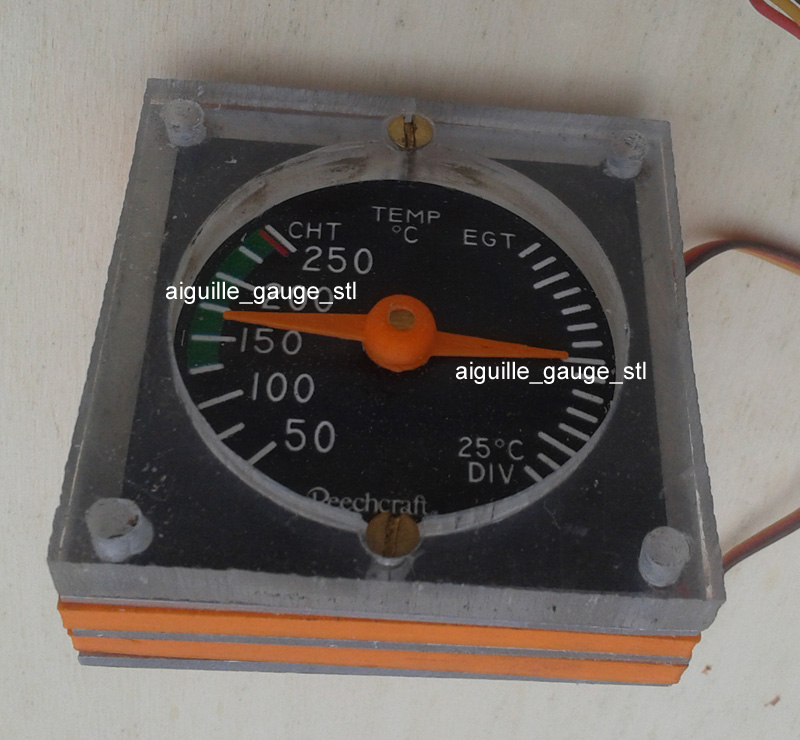

Pour plus de facilité avec les alésages des roues dentées, les axes ont un diamètre de 4, y compris les axes creux qui eux, accueillent un axe de 3 mm de diamètre.
Voici la sérigraphie:
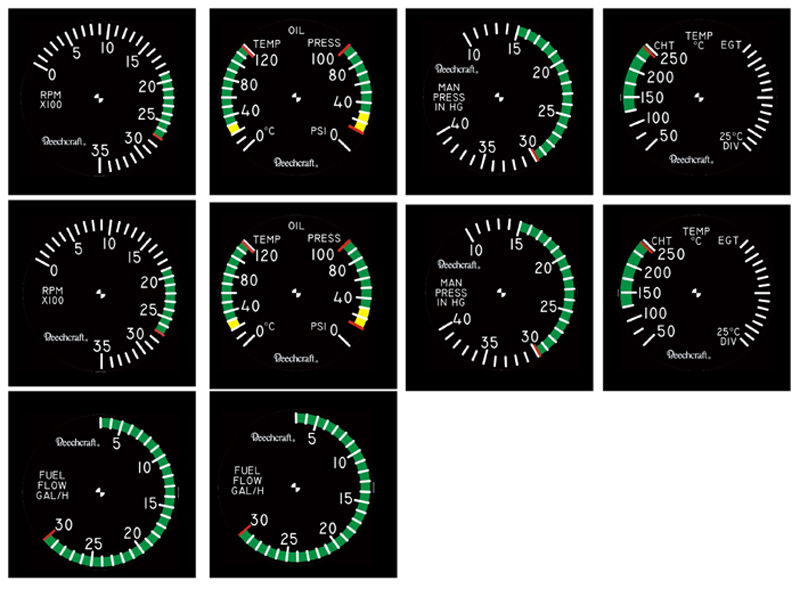
et les bezels:
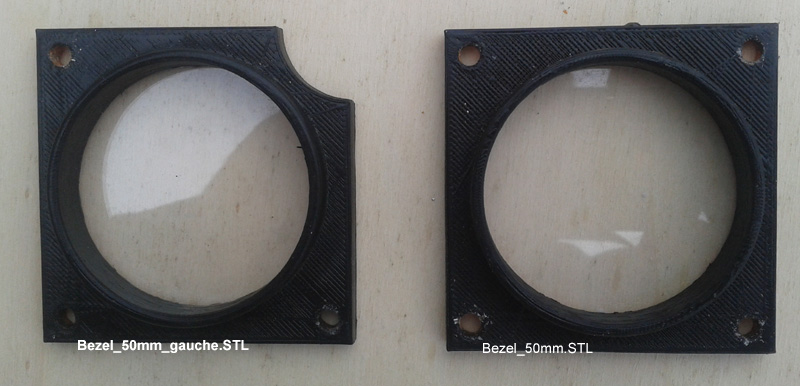
C'est tout pour aujourd'hui.
A bientôt.
Jean-Gilles